ah I want to walk you through the layout
for this project and I've got four legs one cross beam this is the main beam
that goes across joining the four legs like the hub of the legs if you like
what I've got is one on three quarters by two and three quarters very standard
stock English size square edge material that the cross beam is one and three
quarters by three and three quarters so basically that would be our equivalent
of a four by two and a three by two in the Americas that would be a two by
three and a two by four but the sizes are different so what I wanted to do is
lay this out in such a way that it would be very visible for you and what I have
is a second hand piece of plywood of which this edge is rough sawn finish not
machined this is being crosscut by hand and it's a bit uneven this one is a
machined edge so I can rely on that so to get the square edge just in case you
don't know how just take a point on here any arbitrary point just four or five inches
in from the end here and make a mark and then measure from that mark any multiple
you're going to measure multiples of three four and five so I'm going up here
in 6-inch multiples and that's going to be 18 inches and then I'm going to come
across here to this mark and that's going to be 24 inches ignore this line
because this line came after this so then I take my tape measure and where I
measured up here to make this line which was going across this way I took another
line from this point here so I set this onto that mark and I marked this one and
this one's going to be 30 inches so that's five multiples of six in other
words so I had 18 24 and 30 now it could be 15 20 and 25 it could be easy
multiples like that so any of those and where that intersection takes place here
that's going to be exactly 90 degrees to this so then wherever I started this
from here I just take a straight edge like this and strike the line and that
gives me a perfect 90 degrees this is dead on 90 degrees so that works very
well if you don't have a square edge if you've got a machined edge here and the
machined edge here just use those that's perfect what we're going to do the
overall height of my sawhorse is is 26 inches that's a good kneeling height and
I can cut it down I can't go any higher because of who I am and you make these
to suit you so measure up 26 inches here and 26 inches anywhere along here just
to give you a parallel line and I'm going to put mine I've cut these two
lengths so this is the the right length of 30 inches I'm going to put this on
that line there so I'm on the line here and I'm on the line here and I am flush
here on the end with this line here so in other words that would represent this
part here that would represent this in relation to this part so this is
perpendicular to the floor so when I stand on here or kneel on here is not
tipping the sawhorse away from it so that's this one don't worry about this
don't sweat it just yet I've got a second piece of wood with a square edge
here and I'm going to put this on my line here at the bottom and then I'm
going to take the actual leg and I'm going to measure in five inches from the
end of this piece of wood here on the bottom edge here like this that's going
to mark the start position for my recess that I'm going to put in here I'm going
to make a recessed housing so this goes on this line and this is goes at the
bottom corner here so I'm dead on this bottom line hang on I need to move over
just over there alright so this goes here and that's giving me the actual
splay that I need for the recesses so in other
words now when I actually cut the recess this will end up in this direction too
so it forms a sort of a triangle which is the chart that which is supposedly
the strongest geometric shape used in engineering and this is engineering in a
sense so now here I'm going to make a mark across here just to give me a
visual line here and going on the inside and that's going to give me the position
of this recess in relation to the leg I've got the sliding bevel here I slide
this up underneath here and I set this to that angle can you see so I've got
that set so give it a turn and now I can use this to establish my actual cut
lines for doing the recess so there's my pencil line I can go on here now make an
initial knife cut here and then I can take my material that I'm using for the
actual leg slide it up against the bevel and make a knife wall just as if I'm
reaching under this corner and already I can see a slight discrepancy between the
pencil line and March will cut line so my knife goes here and I make a light
pass just like this that's giving me the cut line that I need now I'm going to
put the bruising on the waste side this is the waste side here this goes here
like this and those are the cut lines for my recess very simple now I'm going
to take my square use the pencil as temporary guide line go on to the knife
wall line and make a mark here and here and I'm also going to mark this here and
here because I want the same on this other side on the underside I use the knife wall as my registration point here and
here though I do mark these at the same time because that's giving me the exact
line set a marking gauge to half an inch deep and you could go less if you've got
narrower material you could go three-eighths of an inch deep I'm going
a little bit deeper because I've got a good broad top piece here some very hard
wood this goes in between those two lines and it wouldn't matter if you went
past the line particularly this is a sawhorse so just trail that pin like
that let me thicken that in for you so you can see where I am flip over and do
the same from this top face so this is the top edge of my saw horse so this
comes out and the same on this one now then you can from here on you could rely
on this this would give you the angle that you need for the shoulder lines
here if you cut line to the say here one two one two and that should correspond
with your leg here which in this case I'm about half a millimeter under which
is fine because I would just take a shaving off the piece of wood for that
distance I wouldn't sweat it at all so these now become the cut lines now if
you want to you can simply measure you know this was five inches from here to
here if I remember correctly so I've got five inches here instead of going
through all that pallava again you can just simply mark this
make a visual wrong way make a visual here drop your piece of wood on purely
the pencil line is just to give you a sight line really that will be more I'm
going to go here well here create my knife wall more heavily with the second
pass and then very heavy with the third drop this on here light pass I'm turning
it round so the bruising goes on the waste side of the wood into that cut
line so I listen for that click drop in here like this and now it's exactly the
same as before use your pencil like this this is my top face this is the
underside run your gauge lines half an inch there we go so these are my depth
lines for my recesses and now we're going to cut those with any housing dado
so I want to know which is my top so this is my top base I'm going to mark
this now just to remind me because this is going to be the visible place and
even though it's a sawhorse I still want to be careful about how this comes out
so now we'll cut the recess and I'll show you how to do that I just took the first one that I made
or laid out against the second one and I transferred the lines directly from it
and then I checked to make sure the recesses were the right size by taking
that directly from my material for the legs so there may be some slight
variance in the leg width and you have to be guarded to make sure you don't
just automatically do everything the same when you're working with um tools
but it's very easy to work this way so I put these two together use this as a
datum point and I transferred all my lines that way so that's how I've set
the second one out so I know they'll be the same so I'll set that aside and
we'll recess this one so just check yourself because sometimes you're
working with this material and you put your layout line this way and you've got
these going in the same direction something's wrong we should be coming to
a point like this so we're going to take this out this out this out and this out
this is a housing joint we've already got the cut lines directly with deny so
now into the knife wall here I can't emphasis would be easy to do on a
machine but the other part the counter part that goes into the leg the work we
do on the leg is very different so we have to consider this because this makes
woodworking so simple I made the recess to drop my saw in as I usually do just
notice that so right up against the knife wall and now work exactly no
longer thinking about the angle now work directly to your square line this way
down to the line I've marked with the top so I know on the top I can't go past
my line on the underside it won't be seen if I go past my line I'm going to
work towards being accurate now you can take a few more out like
this but only if you want to you could leave it solid and not do this I'm going
to go in here now take this down here nice and this just takes out the bulk of
the waste like this then I go with the heel of my hand here follow the line of
the recess like this just take our nudge out those pinnacle points now this is my
top face so I can actually go all the way through on that underside and not
worry too much as long as I'm careful I guess the question comes now would I use
a router to guarantee the depth probably not I'm going directly because this is
so narrow and it's less critical so I'm writing my cut line and I'm following my
gauge line exactly because I want this to be crisp on this top edge it's going
to be seen so I take this out here so I've got an incline now from this
side now I'm trying to go level here like this you see inside here so this is
level I've got a crisp joint line here crisp here crisp here now I come from
the underside edge so it's nice to have these reference phases where you can
visualize what's critical so I know I'm flat there I'm perfectly
happy on this here I'm going to come in here and I'm just going to pare down
this one trying not to undercut because it's visible this just cleans out the
saw fuzziness left by the saw there and that's how we cut the recesses so I have
seven more to do if I'm making the two sawhorses so we'll get back together
when this is done this let me give you one quick lets see how this goes there we
go so I'm dead on there's no gap either side I'm perfectly happy with it that's
what I was looking for and that's what we'll do on the others
I've got all my recesses cut for both sawhorses
set one aside I'm going to show you how we get this compound angle and layout
for it I've got each of my legs are numbered for the recesses so this will
go into this one hopefully and what we're going to do is we're going to aim
for this point here to be flush on this top edge you could overhang slightly you
know 1/16 or two mil so I'm going to drop this in here get this fully seated
down onto this line all the way down like that and I've left it past can you
see that's adequate and the reason I've left that passed is so that when I come
to saw cut this the saw will take the full end of that piece off when I come
to this is nine inches this stick and it goes under the leg knee it to the end it
doesn't have to be right on the end but I've got it flush with the bottom edge
of the piece of wood I've got flush with the bottom corner here and I want to
bring this around here like this so this now is lying flat on my bench top and
this leg is elevated nine inches so I'm going to make sure this is fully seated that feels great
this is good and the both edges of the bed of the sawhorse crossbeam are down
so there's no gaps on either side that's very important the next important thing
I'm just going to use a 3/8 chisel here for my space here and a good sharp pencil
that gets tight into the corner like this so this goes here now you can just
use a 3/8 packing if you want to this goes here and that's giving me cut line
I go onto this other side here and I do exactly the same no different so I've
got these two lines now just like there's one and this is what
we call a scribe cut and it's got one on that side like that you can see inside
here how the stick was keeping this distance up that's because I wanted that
splay now just to make sure I don't bump here I'm going to put the stick back
under here back to that point so that's my datum point now I'm going to go with
a straight edge on the underside of the beam across beam like this of this now
goes under here I'm pushing it with my thumb to get the exact line that I want
and then squeeze this here this line comes here that's going to be the seat cut
I do the same on this side just the same way exactly the same and I
get this seat cut we take this take this out so now we have this compound line
which is kind of like a bird's mouth oops this comes here see this and this ever
they're different heights from the top this is what's going to undergird the
crossbeam so when I joined this point to this point this is where I get that
compound seat cut and this is where you start to see that it's not impossible
but it's tricky on the top edge here we have two more points we want to connect
so I've got this one here and this one here now another straight edge across
here this isn't perfectly parallel to the outside edge and it doesn't need to
be so now you can see that wasn't
complicated if you try to write this down in a book it might be more
complicated but this is so simple because you can see it now you can set
your sliding bevel to an angle that compensates for that just so you can have
a knife wall to work to if you want to so I'm going to do that here like this
and that just gives me a hard line to pull my knife to this goes here so this
is cross-grain cut that's why we're doing this I'm going to sew down those
that shoulder line I'll go with a tenon saw dovetail saw just to refining line
and lead I've gone across now I'm going to follow the angle here like this
now could technically go just from one side like that but I'm going to go from
both sides it is a single plane it's in one plane so it would be the same but
this just gives me extra confidence I'm following this line on this side now
down into the line the pencil line try not to go past the line just weakens it
if you do it wouldn't be seen actually but then I go back to my you could use a
tenon saw if you've got a good big one if you don't just use a handsaw I'm going
to cross the top here keeping to my line like that so
I've left my line in and I go down a little bit and start dropping my hand
with each cut here I want this to be as accurate as I can get it off the saw if
possible so I've gone corner to corner I've got my line on the top and I still
have my line in here so I saw exactly to the line flip it around and do the same
here using that to guide you going off a little bit there we go so I'm listening
for the sound now I'm coming into that shoulder line there we go there's my seat cut here shoulder line
let me just clean up a little bit not much it looks very nice so you just take
off any hump there good and tight there pare down on the fuzzy bits just so it
seats properly don't undercut it because you will lose the full property of the seat cut now
let's see where that goes because if this one fits which we know it will
right then we can do all three others the same way this is D and this is D
this goes right under here just line up that shoulder just feel a little bit
tight I'm right here this is probably a good idea just take
your chisel and give it just a slight leading oops not that much can't go
that way can you here bevel down give yourself with just a slight leading edge
into that so you don't split off this outside edge see if that helps because I
want these tight just tight as I can get them there we go nice that's really looking
pretty good but I need it to go down into the seat here
can you see underneath there Phil so just take a block, tap this down on to that seat line it's got it
and now we can seat this into each joint fully just like that nice tight along
this edge seat line I need to go down again here till it's nice and solid
there she blows that's great so now we do all the others and we're ready to put
this together so now you can start to see how the sawhorse is going to sit in
a little while you've got your splayed legs going in both directions gives it
great stability very solid work but I'm saw horse that's great so we'll do the
others and then we'll get back together we are about to assemble the legs and
fitted them all so they all seat perfectly fine after a little bit of
fine-tuning just with the chisel on the shoulder lines they came up I didn't
have to alter the shoulder lines just to pare down on the fuzzy bits really so
this is where we offer the legs and we have to really do one at a time because
even if they're tight the weight of the leg will usually drop down so you just
screw one in at a time and we go ahead and put this in the vise compress it
down into the recess work it so you get your shoulders in place and then if all
else fails use a big hammer right that's it really so what I'm going to do is I'm
going to make a sight line across the underside of the crossbeam here so this
just there so then if you took a chisel say five h's or you could measure up
from that line just make a line here that will mark the bottom for this wire
you could either way really and then this one wants to go in the middle of
the beam here those are my sight lines for my drilling holes I'm using a 1/8
pilot hole to go through both up all the way to full depth of the drill bit so
this allows me to align the drill bit up with the perpendicular to the main body
of wood not to the leg so it's going into a good body of wood inside there
then I've got I'm using sixty millimeter screws and I want it I want this bit to
take the full shank of the screw including the threads I'm going to
separate this so that I don't drill into my pilot hole and then drill through
this you can put this in the vise to safely oops the bit will just follow the
pilot hole where your pilot hole countersink here make sure that
countersink will take the full head of the screw and sink just a little bit
below so that will go below the surface you don't want the screws flush or
protruding in case the saw slips then we're going to glue this and we go
on the shoulder line too just to give it something to bed to and more on here do
you need to do the sidewalls you can do nothing wrong with that make sure your
shoulder line is up tight you get a little bit more movement now because the
glue will work as a lubricant shoulders up tight long as you don't have a gap
under here you should be good to go these will go now now I should have been
ready with the screw bit I'm going to let that seat I'm not
taking it all the way yet like this like this and then I want to check on the
other side just to be sure I don't have any gaps happy with that and I'm happy
inside here that I don't have any joint any anything missing there so I'm going
to do the others now I'm going to keep you with me I'm not going to just go off
and do the others because there may be idiosyncrasies to each one that might
help you when you're doing yours so try them before you apply the glue I've
already tried these I do know that they go but you have to put them in anyway to
get everything ready for drilling I want to cite these I'm going to do two
opposite so this one here this one is 5/8 up just like that i did
something slightly different to the last one I went deeper with my pilot holes
these are all as tiny nuances the things that you do that we often take for
granted really here's one thing I didn't do yet and I probably would do it before
I got to it I would take the iris off all the legs here half-a-dozen strokes
just like this just to make it more comfortable I did do it on the crossbeam
already I already finished that one out now we're ready to give it a little bit
of glue I did it again didn't I this is a little
bit tricky oh good just take a bite and we can tight it in a
second perfect excess glue goes under the bench we're good to go on the next one's a
little bit more awkward here if you have a bench where the vise is not protruding
you'll see what I mean when you get to it what we'll do here we're going to put
this in sight it with the one underneath not that we can do much about it remember this time gets very close to the finish finish
line so we'll leave that to dry and then
we'll do next bit which will be the gussets at all four points now not quite
we're going to show you how to describe that to make it perfect so that's the
next step now I'm going to do the gussets first to make sure that the legs
are spread exactly and things like that but that's the next stage you
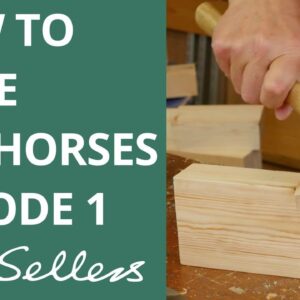